Australian luxury motor yacht builder, Riviera, recently hosted a team of experienced marine technicians and engineers from its worldwide dealership network for a three-day training and service academy.
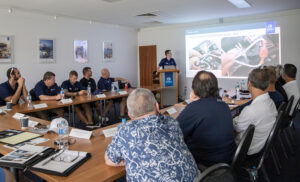
Senior Riviera technicians hosted a range of classroom sessions during the three-day service academy.
They travelled from the Americas, Europe and Asia, eager to grow their knowledge of the latest systems, technologies and build processes being employed on the new era luxury motor yachts.
The service academy took participants through the entire yacht production process, from hull lamination and engineering through to anti-fouling, at Riviera’s 16-hectare (39.5 acre) state-of-the-art facility on Queensland’s Gold Coast.
Chris Attard, Riviera’s Dealer and Owner Care Director, said the three-day academy comprising more than 10 separate workshops, as well as extensive tours of the facility, is a part of an annual program conducted by Riviera focused on enhancing the skills of its dealer network teams.
They were given a detailed understanding of the new product development process including a confidential tour of a new yacht in the early stages of development.
They also undertook an extensive review of Riviera’s latest safety systems, vessel care, maintenance and system connectivity, designed to make boating with Riviera easier, safer and more enjoyable.
The final day of the program included sea trials aboard three Riviera yachts including the newly launched 46 Sports Motor Yacht.
Matt Mrozinski from Lake Michigan Yacht Sales said: “We have been a Riviera Dealer for 16 years and I have visited Coomera a number of times. On this visit I was extremely impressed by the significant investments and improvements the company has made right across the site from technology to buildings and processes.
“The training was very technical, which our team greatly appreciated. Seeing exactly how the yachts are built today, being able to touch and observe the entire process was very beneficial. This latest training and knowledge sharing allows us to better serve our customers.”
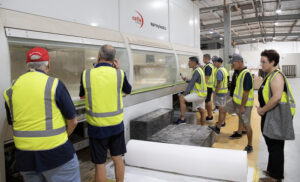
Riviera’s robotic varnishing system enhances the work of master craftsmen to achieve a world-class finish.
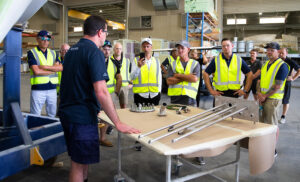
Delegates learn how Riviera’s strong and safe fuel tanks are engineered and constructed.
Greg Glogow from Sun Country was deeply impressed by the Riviera facility, and its level of presentation, technology and growing scale.
“I have been in the marine industry for more than 30 years and this is the best facility I have seen anywhere in the world.
Randy Buckell from Emerald Pacific Yachts commented on the extensive detail of this latest training academy.
“This additional knowledge regarding the new batteries being utilised, the inverters and charging systems was very helpful. We were able to meet and talk with Riviera’s engineers and technicians and further our knowledge.”
Randy’s business partner Brett Aggen said this latest round of product knowledge was vital to the dealership network’s capabilities with customers.
“Everyone can see and touch a yacht. Understanding the technology so often hidden on board is important in being able to answer customers’ questions with confidence and provide assurance and, if required, service assistance.”
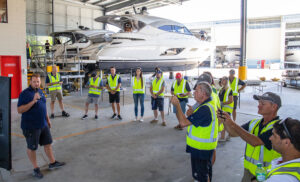
Pre-delivery and systems checks were covered in detail.
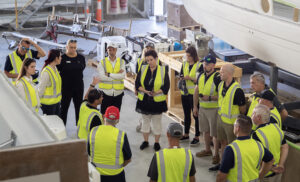
Each precise Riviera engineering step was covered in the academy program.
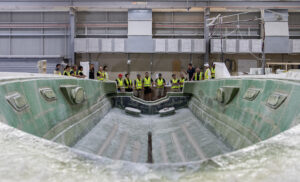
Riviera’s unique hull lamination design and specification achieves strength, safety and weight savings.
Chris Bingham, also with Emerald Pacific Yachts, said seeing the scale of the Riviera operation was eye-opening.
“I was impressed by the efficiency of the plant and how much effort Riviera takes in eliminating waste and focussing on the reliability of the yachts. They undertake 1,700 tests during a build before the yacht is handed over to a customer.
“The yachts are complex systems and it’s great to know just how meticulous the build team is.”
Kenny Brown from Sun Country said he was already familiar with much of the new technology including Garmin and CZone.
“The seminars were very useful and the Riviera team was very open to answering all our questions,” he said.
“Being able to have the time to get to know and talk with the Riviera technicians was very useful.
“I thought the training would be good – but it was truly amazing.”
Anthony Vigliotti from OneWater Group appreciated the in-depth factory tour.
“It helps us greatly to understand how the yachts are built. I was impressed by the processes that drive each build.
“The fact that Riviera manufactures even its own small parts sets this organisation apart. We will take much of the Riviera culture back home with us.
“These are yachts built by people with pedigree!”
Riviera Australia owner Rodney Longhurst thanked the international team for their enthusiasm and for their dedication and support of Riviera owners around the world.
“Our worldwide network of representatives is the face of Riviera and we are extremely proud of your efforts,” Rodney said. “We are appreciative that you have set aside your time to travel, for some a journey half way around the world, to update and expand your Riviera expertise.
“Your dedication to ensure the best experience possible for Riviera motor yacht owners has never been stronger.”
For more information visit www.rivieraaustralia.com